On a snowy December morning in 2019, I find myself at the gates of Rittal’s new Smart Factory in Haiger, in Middle Hesse. The world’s leading system provider for control cabinets, power distribution, climate control, IT infrastructure and software & service is creating a smart factory at its new plant – the world’s most modern production facility for compact control cabinets and small housings. Today, I am part of one of the first small groups, which have the opportunity to tour this unique digital manufacturing facility.
The plant, which is fully aligned with highly efficient Industry 4.0 structures, is not yet 100% in production. Big Data – a multitude of data from machines, actuators, and sensors are still being integrated into monitoring, data and system integrations are taking place in parallel, and an expert team of development engineers and service technicians is analyzing and clustering lots of data for the large Industrie 4.0 format of visualization. The context then turns the data into the immediately provided information. The goal is to manufacture around 9,000 compact control cabinets and small enclosures per day in a highly automated way in the new factory halls on 24,000 square meters with more than 100 new high-tech machines, plant components, and IoT platforms.
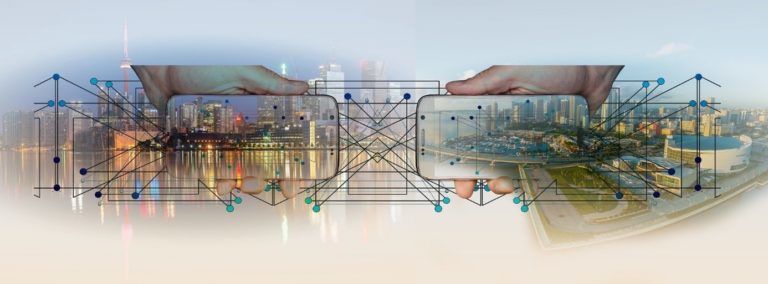
What is Industry 4.0 actually (for us)?
The term Industry 4.0 was first introduced to the public in 2011, exactly 10 years ago at the Hannover Messe. A working group ultimately gave rise to the Industrie 4.0 platform, an alliance of the industry associations Bitkom, VDMA, and ZVEI. Since then, the Industry 4.0 platform has been further expanded and the goal is to further develop the content associated with the term Industry 4.0 in dialog with unions, trade associations, companies, science, and politics.
Industry 4.0 – making relevant information available
For us, Industry 4.0 is a new level of organization and control of the entire value chain over the life cycle of products – from the idea to recycling. Individual customer requirements arise in discrete manufacturing and a study by International Data Corporation (IDC) from 2019 shows that 42% of Industrial IoT projects in the German industry are implemented precisely where a high degree of product customization (up to batch size 1) is required in industrial production.
The basis is the availability of all relevant information in real-time through the networking of all the instances involved. The challenge here is the ability to derive the optimal value creation flow from the data – at any time. The connectivity of people, objects, and systems results in value-adding networks. They are dynamic, real-time optimized, self-organizing, and cross-company.
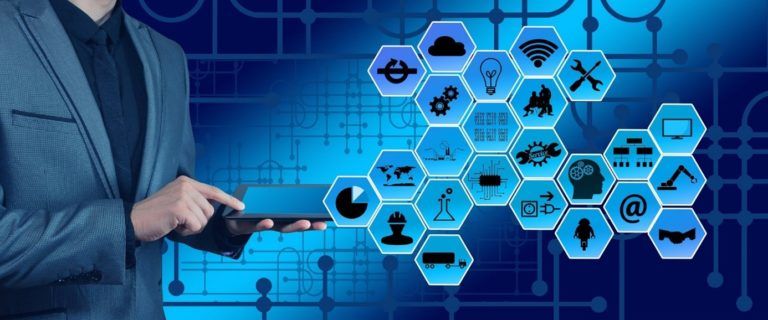
What are the major challenges in the Industrial Internet of Things (IIoT)?
In contrast to the Internet of Things (IoT), the Industrial IoT does not focus on consumers and users, but on industrial processes and workflows. The goals of Industrial IoT are to improve operational efficiency, reduce costs in production, speed up processes and realize new business models.
Back in Rittal’s new digital factory. Driverless transport systems approach me, drive past me under sensor control and automatically take over the transports in the factory. I feel like an extra from a Star Wars movie. I start talking to an engineer from process automation. He is totally enthusiastic, somehow also proud to be working on this 24,000 square meters digital stage.
Formerly analog, now digital
“Previously, we had a large number of isolated solutions of systems, machines, and plants. We lacked transparency about orders, processes, and production status due to a lack of data availability. And then an incredible amount of paper, paper-based process steps, and inevitable media disruptions,” the engineer said. “There was a lot of ad hoc planning and communication instead of structured planning. And lastly, it’s about more precise control of how much electrical power, water, and other resources are being used, when machines are running, and how much they’re producing.”
Connectivity – connecting people and machines
I agree with him, and where the individual manufacturing processes of cutting, edging, welding and painting used to be carried out transactionally, sequentially, and independently of one another, in the smart factory, all people and machines are increasingly integrated into the manufacturing execution system (MES). The individual assemblies are automatically brought together at the end to form the finished product. In the process, the machines and handling systems, the automated guided vehicles communicate with each other and with the higher-level process control systems. In this way, the machinery in the production process automatically adjusts to the workpieces and assemblies to be produced.
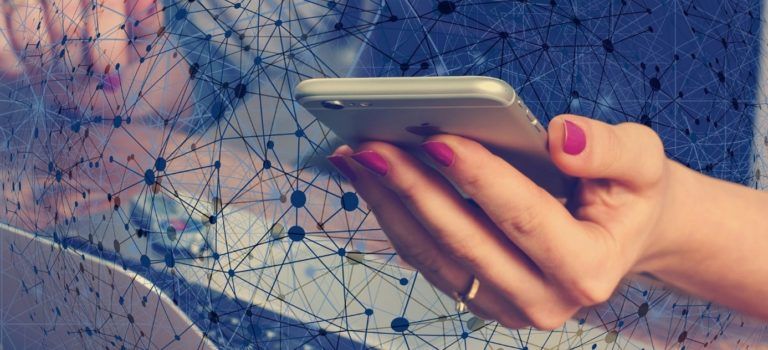
5G, Edge Computing and AI/ML – new technologies in Industry 4.0
I meet a young man from IT. He tells me a lot about Big Data and new technologies that will be used in the future. The entire machine park constantly supplies data about the control system and the current operating states. In the future, this data will be collected in an edge data center at the plant and analyzed with applications from a sister company. This will form the basis for industrial analytics. With the help of knowledge-based systems based on artificial intelligence (AI) that continuously learn – machine learning (ML) – downtimes are reduced, maintenance is planned in advance (predictive maintenance), and disruptions to the sophisticated production process are minimized.
According to IDC estimates, these new technologies such as 5G, edge computing, and AI/ML should be used and deployed to lay the foundation for new business models and services in the long term, which can either be provided independently or integrated into ecosystems. Developing these ecosystems, establishing corresponding partnerships, and determining generally accepted standards should and will be one of the central tasks for industrial and industry-related companies in Germany in the coming years in order to remain competitive.
5G – data processing at 10 gigabits per second
In the meantime, the control cabinet specialist Rittal has become one of the first industrial companies in Germany to receive a 5G frequency allocation. A private 5G mobile network was already installed at the new plant in Haiger in 2020. The first pilot projects, for example in production monitoring and analysis, are already being planned.
Rittal wants to install and commission the 5G mobile network in its Smart Factory in Haiger in a real production environment as quickly as possible. The new 5G technology is expected to significantly accelerate and simplify data traffic – for example, in the video-based comparison of unit numbers with stored order data and in the step-by-step implementation of data analytics for preventive maintenance. With the new 5G mobile communications standard, data can be processed at a speed of 10 gigabits per second. 5G is regarded as the technology of the future that will enable industrial manufacturing processes to be networked and controlled even better – and thus further exploit the potential of Industry 4.0.
Edge Computing in the industrial IoT
Current cloud computing trends present edge computing as a concept that can revolutionize industrial operations. This is due to its ability to enable unconnected devices, manufacturing tools, IIoT devices, and workstations to collect and process data without having to work with a central database system. With Industry 4.0 and the millions of sensors and IIoT devices powering it, edge computing for industrial IoT will reach new heights.
Edge computing can be defined as providing data handling activities and operations at the source without having to go through centralized network segments. This computing process optimizes (IoT) devices and applications by bringing computing closer to the network edge of these data-producing devices. Depending on the device or system, the network edge may refer to the area where the device communicates with the Internet.
This is also the case at Rittal. In the future, data generated and required on sensors, components, machines or robots can be collected and evaluated faster than before in an edge or cloud data center. The necessary IT requirements are already in place at the new plant in Haiger.
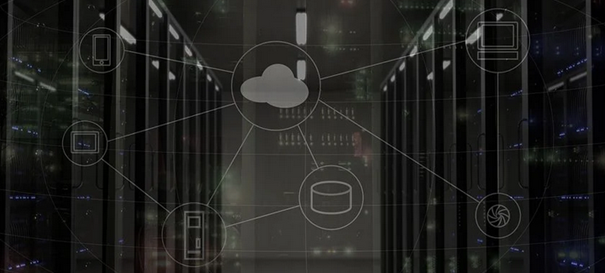
What is the difference between artificial intelligence (AI) and machine learning (ML)?
In Rittal’s Smart Factory, data is generated by over 100 machines. That’s up to 18 terabytes a day. The data can only be evaluated if it is analyzed by artificial intelligence (AI) after it has been collected. And humans play a decisive role in this: Only with humans as systematic trainers do the plants become learning systems – machine learning (ML) – and later intelligent systems.
Computer programs that played checkers
They are one of the earliest examples of Artificial Intelligence. At the Dartmouth Conference in the summer of 1956, it was the idea of AI pioneers to construct a complex machine that would have the same intelligence as a human with the help of emerging computers. This concept is referred to as the “General Artificial Intelligence (AI)”: Machines that have all our senses, our reason, and think like us.
What can already be implemented today is a concept of “limited AI”. Technologies that are able to solve specific tasks as well or better than humans. An example of this is Facebook’s facial recognition or Pinterest’s image classification. The technologies show aspects of human intelligence. But how does it work and where does the intelligence come from? This is where machine learning (ML) comes into play.
“Machine learning” refers to a cross-cutting discipline of statistics, computer science, and mathematics that aims to construct software systems that can automatically learn from data. A variety of generic learning algorithms have been developed to solve a variety of learning tasks or to gain new insights from data. Machines thus learn complex relationships that humans are no longer capable of in terms of speed and accuracy.
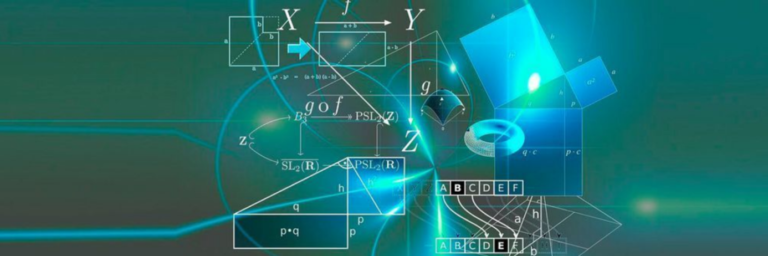
To make the growing flood of data in industrial production manageable, machine learning helps to decipher complex relationships from an immense amount of sensor and process data, to recognize patterns and to generate new knowledge.
Source Code or rather Low-Code / No-Code?
My factory tour of the Smart Factory at Rittal is nearing its end. Almost at the exit, I look over the shoulder of a technician who is making some programming adjustments to the source code on a process computer. What used to be a familiar concept to IT professionals is now indispensable in the field of software and application development. From the automotive industry to pharmaceutical companies – from medium-sized companies to global players. They all use it and the application possibilities are almost limitless.
We are talking about Low-Code / No-Code
Digital processes and applications have to be faster, more powerful, and more (cost)-effective. The premise of digitalization applies to all companies because, in times of rising requirement profiles, an increasing shortage of skilled workers and overburdened IT teams, a Low-Code or No-Code automation platform is often an effective means of saving development time, reducing costs, and always keeping one’s own applications up to date. For IT and business departments, in particular, this offers the opportunity to meet the high demand for applications and other activities.
Where is it going now, the future journey for Low-Code / No-Code?
IT analyst Gartner predicts that the creation of low-code applications that include No-Code will account for more than 65% of all app development functions by 2024. By 2024, 75% of all large corporations will use at least four low-code development tools for activities in both IT application development and Citizen Development. Forrester Research predicts that Low-Code’s market share in business applications will multiply from the current eleven percent to more than 30 percent within the next few years. In a white paper on the subject of low-code, IDC sees greatly shortened development cycles and advantages through productivity increases of up to 25 percent.
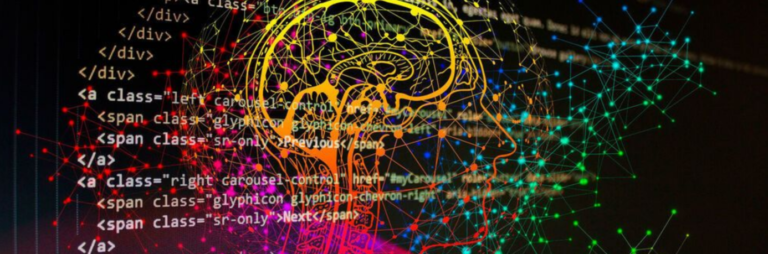
Individual software solutions are in demand
In just a few years, low-code and no-code development technology has become the hallmark of development efficiency and a clear competitive advantage for companies. Instead of the tedious coding of individual programming lines, low-code works with the help of a modular principle. Prefabricated building blocks replace text-based coding. This saves companies a lot of time and money – and relieves the tight resources of in-house IT teams. The modular building block principle of low-code development uses application designers, graphical methods, and libraries to create individual software solutions and business process applications. In this way, new functions with increasingly complex requirement profiles can be implemented in a short time.
COVID-19 and Industry 4.0
Today, I still often think back to this impressive Industrial IoT experience in Rittal’s Smart Factory. Rittal is a prime example of Industry 4.0 in action, and even today in COVID-19 times, the Industrial Internet of Things is more than present. Currently, many companies see key advantages in the Industrial IoT to overcome short-term challenges. According to a recent IDC study, 59 percent of respondents are planning new IIoT projects. COVID-19 is certainly slowing down some companies at the moment, but for others, it is the moment when their investments in new technologies and especially in Industrial IoT pay off. As the results of the study show, the crisis is also a wake-up call for many to carry out long-needed modernization.
Because one thing is clear. The importance of Industry 4.0 for Germany cannot be overestimated. Industry 4.0 is the prerequisite for maintaining the competitiveness of the German industry and thus securing jobs.
The opportunities are huge, and nothing better can happen to Germany, a location that is poor in resources and rich in know-how, than digitalization in the industry sector.
Links
https://en.wikipedia.org/wiki/Fourth_Industrial_Revolution
https://automationspraxis.industrie.de/industrie-4-0/rittal-smart-factory-fertigt-schaltschraenke/
https://automationspraxis.industrie.de/news/rittal-pionier-beim-5g-mobilfunk-in-der-produktion/
https://www.industry-of-things.de/iot-basics-machine-learning-in-der-smart-factory-a-698047/
https://www.industry-of-things.de/low-code-ist-integrativ-automatisiert-und-smart-a-960267/
https://www.mendix.com/de/resources/gartner-magic-quadrant-for-low-code-application-platforms/